The pandemic put strain on our economy as well as manufacturing. The shut-down of businesses during that period has left more demand with limited supply as companies struggle to keep up. That has also put higher prices on what is available on the market. The entire collection of issues has drove construction projects to a near halt.
Bast fiber is a natural, strong, woody product found in vascular plants like hemp. A material that is much considered a byproduct of hemp plants. History of such fibers can trace back 32,000 years. Very commonly used in our own American heritage with the founding fathers.
The cost of making bast fiber is low, since it is generated from organic resources that are easier to regenerate than trees and other common fiber materials. The annual hemp crops growth cycle is around 100 days. Using the product in a compressed manner with additives can produce a material that is resilient and strong enough that it can be used for decking, railing, fencing, siding, and other structural lumber needs, especially when added with chemical formulas that help create a composite material. Using other bio-friendly materials like sawdust or recycled thermoplastics create a viscous compound and varying other chemical formulations can also help make all-weathering material, or fire resistant.
Hemp fiber can also be spun to create roping material which can be woven, knitted or used for cloth opening up an entire realm of possibilities. The fiber is mildew resistant, lightweight, and easily laundered for upkeep.
The major process of creating fibers comes during the retting. The separation of fiber bundles and placing them flat in the field after being harvested and allowing the dew and air-humidity to aid the process. The entire method allows the enzymes within the fibers to produce microorganisms that attack the pectin’s and therefore glue the fibers tightly together. This impactful step is very low cost as it requires no machinery and simple manual labor. After the retting process the bundles are either spun to create a long, continuous rope, or broken into smaller bundles to work into other materials for composites or hempcrete.
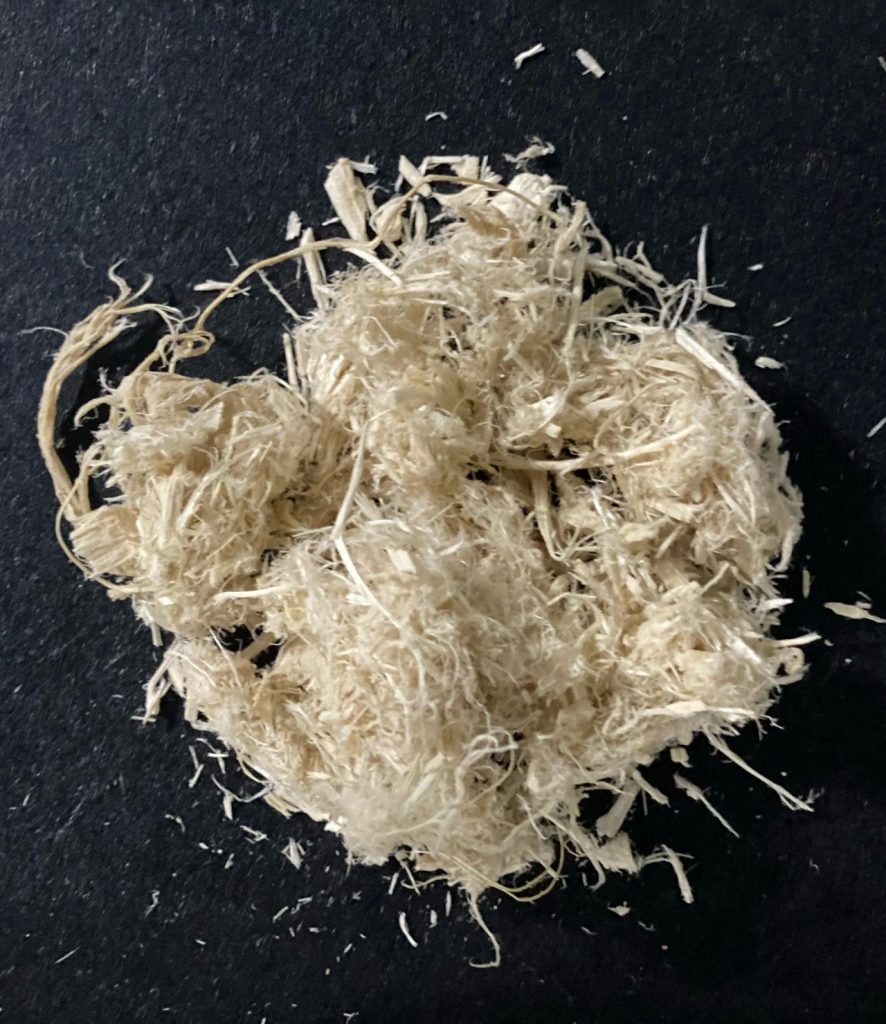
Popping up around the country are fiber processing plants, currently opening industries in Kentucky, Colorado, and Minnesota – also creating new jobs for many. Down in Texas, Dallas and Wichita Falls announced that they were opening the largest hemp fiber processing center in the United States. The Texas plants will process and cottonize the hemp product on a commercial scale, with goals to produce product at the scales of China. These processing plants are located next to their raw material housing units which streamlines the process and is starting to take over the market for the new, sustainable, green product. It’s within reach that the United States can one-day lead in the global market for hemp production. The opportunity is still yours for the taking in Michigan, with no known plants to exist in the state as of July 2022. The market is there, and the current economy is pursuing cheaper, eco-friendly solutions. Be a part of the future!